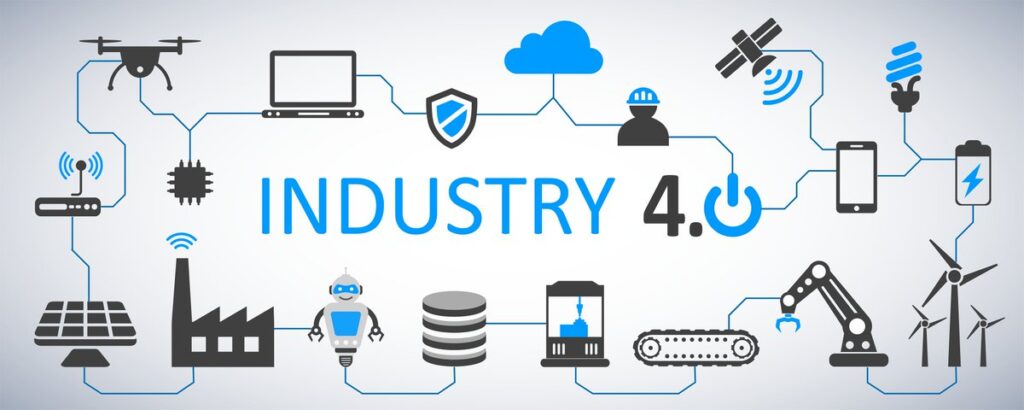
Industry 4.0 focuses on using digital technology to gather and analyze data across machines and business systems – enabling faster, more efficient processes. Many organizations are implementing changes today and preparing for a future where smart machines improve their business with increased productivity and efficiency through better analysis of the data.
Here are just a few of the possible applications:
Internet of Things and the cloud: A key component of Industry 4.0 is the Internet of Things that is characterized by connected devices. Not only does this help internal operations, but through the use of the cloud environment where data is stored, equipment and operations can be optimized by leveraging the insights of others using the same equipment or to allow smaller enterprises access to the technology they wouldn’t be able to on their own.
Optimization of logistics and supply chains: A connected supply chain can adjust and accommodate when new information is presented. If a weather delay ties up a shipment, a connected system can proactively adjust to that reality and modify manufacturing priorities.
Predictive Maintenance: Predictive maintenance is a technique that uses condition-monitoring tools and techniques to track the performance of equipment during normal operation to detect possible defects and fix them before they result in failure. IoT allows for different assets and systems to connect, work together, and share, analyze and action data.
Digital twins: In essence, a digital twin is a computer program that takes real-world data about a physical object or system as inputs and produces as outputs predictions or simulations of how that physical object or system will be affected by those inputs.
Autonomous equipment and vehicles: There are shipping yards that are leveraging autonomous cranes and trucks to streamline operations as they accept shipping containers from the ships managed via a central control room.
Robots: From picking products at a warehouse to getting them ready to ship, autonomous robots can quickly and safely support manufacturers. Robots move goods around Amazon warehouses and also reduce costs and allow better use of floor space for the online retailer.
Additive manufacturing (3D printing): This technology has improved tremendously in the last decade and has progressed from primarily being used for prototyping to actual production. Advances in the use of metal additive manufacturing have opened up a lot of possibilities for production.
Intelligent Factories are more flexible, agile and responsive
Intelligence is often driven by device connectivity, the vertical integration of sensor /machine data into a horizontal business process. This IT/OT convergence allows to further automate manufacturing operations. Organizations are gaining increased shop floor visibility, identifying process bottlenecks, and managing operations with greater agility. This, in turn, facilitates smart factory capabilities where rigid production lines are transformed into flexible manufacturing cells – making it possible to shift from mass production to mass customization.
The numbers speak for themselves. Most manufacturing leaders report that Industry 4.0 has or will lead to positive change:
- Increase productivity
- Increase profitability
- Improve product quality
- Increase customer satisfaction
- Improve machine reliability/uptime
- Increase worker safety
To solve challenges, and improve business productivity and profits with the use of barcode, RFID & IOT technologies (key components in IOT/ Industry 4.0), please talk to our team of solution experts with a track record in delivering value for manufacturing, logistics & retail businesses!
Author: Gaganish Mittal
Date of Creation: 5th July, 2020